think im loseing steps
-
- 1 Star Member
- Posts: 11
- Joined: Mon Nov 11, 2013 9:27 pm
- Location: March uk
think im loseing steps
Hi iv just completed my plasma table I'm just waiting for a some 10 to 1 planetary gearboxs as atm I'm direct rack and pinion 1.5 mod. So when I'm cutting holes there out of shape I'm using mach3 my steps are only 22.5 ish and I think im loseing step due to my plasma being of a hf type my question is when I put the gearboxs on this should increase my steps thus if I lose the odd step it shouldent really be a big deal and my holes should be alot better. Am I right in what im thinking.
-
- 2.5 Star Member
- Posts: 212
- Joined: Sun Dec 01, 2013 1:29 pm
Re: think im loseing steps
What type of table are you using? Lots of details are needed to answer this. Gantry, accelleration, speed, motors....Also pics would be helpful. The partial step should not affect anything if it is setup correctly. 22.5---is that steps per inch or what is it? Try cutting or marking some thing large. Take the attached file and start on the straight side and finish on the straight to see if the lines meet. If they meet then you are not loosing steps. I have done similar things with a pencil mounted instead of the torch. Try at different speeds also!
You currently do not have access to download this file.
To gain download access for DXF, SVG & other files Click Here
Precision Plama LLC SDB 5x10
CandCNC
Hypertherm 65
Mach3
SheetCAM
the GIMP
inkscape
QCAD
https://www.facebook.com/burtonskustom
CandCNC
Hypertherm 65
Mach3
SheetCAM
the GIMP
inkscape
QCAD
https://www.facebook.com/burtonskustom
-
- 4.5 Star Member
- Posts: 1504
- Joined: Fri Jan 18, 2013 3:19 am
Re: think im loseing steps
First thing is that if you are losing steps, something is wrong and needs sorting out. Correctly tuned / sized steppers should never lose steps.
Your thinking is correct as far as the error reduction goes. With 10:1 reduction drives, assuming the same number of lost steps you have 1/10th of the distance travelled. However using a much higher "resolution" to reduce the effects of something faulty is not a great way of solving a problem.
The reduction drives are probably way too low gearing for steppers. They normally have closer to 3:1. The reason is getting the right balance of speed and torque. Steppers lose torque as they spin faster. Your steppers will now have to spin 10 times as fast for the same speed. I've seen people with servo motors using 10:1 reduction boxes. Tom from Candcnc said after lots of experimentation he worked out the optimal gearing of stepper motors gave 1 inch of travel for 1 revolution of the stepper motor.
Your thinking is correct as far as the error reduction goes. With 10:1 reduction drives, assuming the same number of lost steps you have 1/10th of the distance travelled. However using a much higher "resolution" to reduce the effects of something faulty is not a great way of solving a problem.
The reduction drives are probably way too low gearing for steppers. They normally have closer to 3:1. The reason is getting the right balance of speed and torque. Steppers lose torque as they spin faster. Your steppers will now have to spin 10 times as fast for the same speed. I've seen people with servo motors using 10:1 reduction boxes. Tom from Candcnc said after lots of experimentation he worked out the optimal gearing of stepper motors gave 1 inch of travel for 1 revolution of the stepper motor.
2500 x 1500 water table
Powermax 1250 & Duramax torch (because of the new $$$$ync system, will buy Thermal Dynamics next)
LinuxCNC
Sheetcam
Alibre Design 3D solid modelling
Coreldraw 2019
Powermax 1250 & Duramax torch (because of the new $$$$ync system, will buy Thermal Dynamics next)
LinuxCNC
Sheetcam
Alibre Design 3D solid modelling
Coreldraw 2019
-
- 3.5 Star Elite Contributing Member
- Posts: 593
- Joined: Thu May 12, 2011 4:28 pm
Re: think im loseing steps
beefy wrote:Tom from Candcnc said after lots of experimentation he worked out the optimal gearing of stepper motors gave 1 inch of travel for 1 revolution of the stepper motor.
I believe alot of folks misquote Tom from CandCNC using this same line. He uses a 1" PD gear with a 3-1 belt reduction as an example only to show how to calculate steps per. This should not be used as a gold standard for any build. You see this everywhere however the assumption is wrong. When gear boxes cause missed steps in a stepper based system it is because your running out of your torque range. You can try running with a lower acelleration rate and a smaller rapid speed. 10-1 with a 1.5" PD you should see a acel number somewhere in the 15-18 range with a max speed of 375ipm. It would be safer to run 300ipm rapids.
-
- 1 Star Member
- Posts: 11
- Joined: Mon Nov 11, 2013 9:27 pm
- Location: March uk
Re: think im loseing steps
Will give more details tomorrow but one reversion of my stepper motor is 70.65 mm of travel at the moment so a 3 to 1 reduction is about right for a 1 inch of travel
-
- 1 Star Member
- Posts: 11
- Joined: Mon Nov 11, 2013 9:27 pm
- Location: March uk
Re: think im loseing steps
Thanks for the info Bta plasma im not useing gearboxs yet going to order soon iv used a pen instead of the plasma torch and every thing measure fine holes are round its just when I use the plasma things go out of shape as if the hf frequency is interfering but all the info from every one welcome. As I said above will give more details tomorrow when im back home.
Im new to all this so its abit of a headache but a am enjoying the learning.
Im new to all this so its abit of a headache but a am enjoying the learning.
-
- 2.5 Star Member
- Posts: 212
- Joined: Sun Dec 01, 2013 1:29 pm
Re: think im loseing steps
Perfect round holes are difficult to create. I know I have read a post by Jim Colt somewhere talking about slowing down and other tricks to get round holes. As I suspect it is not a hf issue more likely just a cam/cut setup issue. Also include how thick of material and feedrates.
Precision Plama LLC SDB 5x10
CandCNC
Hypertherm 65
Mach3
SheetCAM
the GIMP
inkscape
QCAD
https://www.facebook.com/burtonskustom
CandCNC
Hypertherm 65
Mach3
SheetCAM
the GIMP
inkscape
QCAD
https://www.facebook.com/burtonskustom
-
- 5 Star Elite Contributing Member
- Posts: 3087
- Joined: Mon Jul 20, 2009 11:18 pm
- Location: North Carolina
Re: think im loseing steps
Round holes require:
- Correct programming of lead in and lead out at beginning and end of the cut
- Tight machine motion (x and y axis) with excellent acceleration, smooth fluidic motion, no backlash or mechanical roughness.
- Proper pierce height, pierce delay, cut height (all of which must occur before any x or y motion starts).
-The ability to freeze the cut height at the correct physical height throughout the duration of the hole, this on all holes under 1" (25mm) diameter.
- slower speed programming (usaually 60% of the recommended contour speed for the material being cut) on all holes under 1" (25 mm)
- And a good plasma using the lowest powered set of consumables that will cut the material being cut.
So hole cutting is not done by the plasma alone. It is a well choreographed dance of all of the above listed functions. I get calls daily complaining about "plasma" issues on cutting holes. In over 90% of them....the issue is not the plasma...in fact the biggest issue is with height control!
Jim Colt Hypertherm
- Correct programming of lead in and lead out at beginning and end of the cut
- Tight machine motion (x and y axis) with excellent acceleration, smooth fluidic motion, no backlash or mechanical roughness.
- Proper pierce height, pierce delay, cut height (all of which must occur before any x or y motion starts).
-The ability to freeze the cut height at the correct physical height throughout the duration of the hole, this on all holes under 1" (25mm) diameter.
- slower speed programming (usaually 60% of the recommended contour speed for the material being cut) on all holes under 1" (25 mm)
- And a good plasma using the lowest powered set of consumables that will cut the material being cut.
So hole cutting is not done by the plasma alone. It is a well choreographed dance of all of the above listed functions. I get calls daily complaining about "plasma" issues on cutting holes. In over 90% of them....the issue is not the plasma...in fact the biggest issue is with height control!
Jim Colt Hypertherm
-
- 1 Star Member
- Posts: 11
- Joined: Mon Nov 11, 2013 9:27 pm
- Location: March uk
Re: think im loseing steps
Ok here's what i'm useing my drivers are TB6600hg, Nema 23 300oz, 5 Axis CNC Breakout Board + LCD Display + Handle Controller, mod 1.5 rack and 15 tooth pinion no gear reduction as yet, one turn of the motor is
70.65 mm or travel. I used mach3 axis calibration to set the steps per unit which gave me the motor tuning step per unit of x axis 22.52234371 velocity 6000 acceleration 1000, y axis 23.7073022 velocity 6000 acceleration 1000.
I'm not using a thc yet but have a floating z axis i'm useing sheetcam to setup my dfx files. I'm useing 2 steppers motors on my x axis gantry now instead of slaving them togeather using mach3 iv took the wires from the x axis
breakout board and put the in to two TB6600hg drivers like in parallel. Iv cut the zigzag test and the picture iv upload is the result and the other is of the holes im trying to cut 16mm and a 50mm in the centre hope you understand what iv put as im terrible at explaining myself.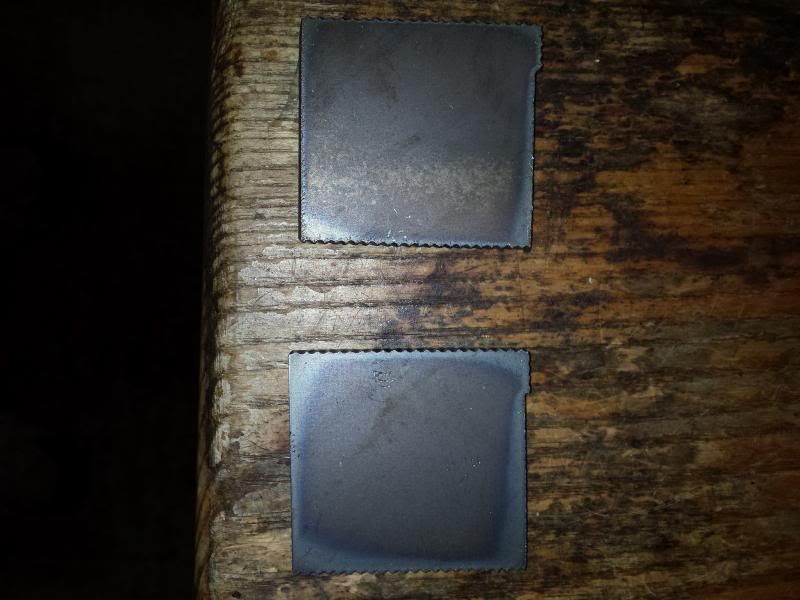
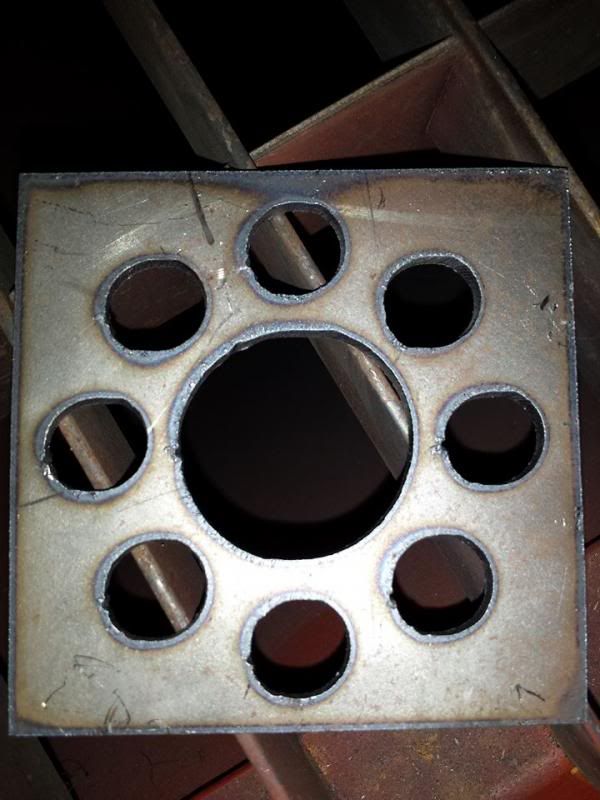
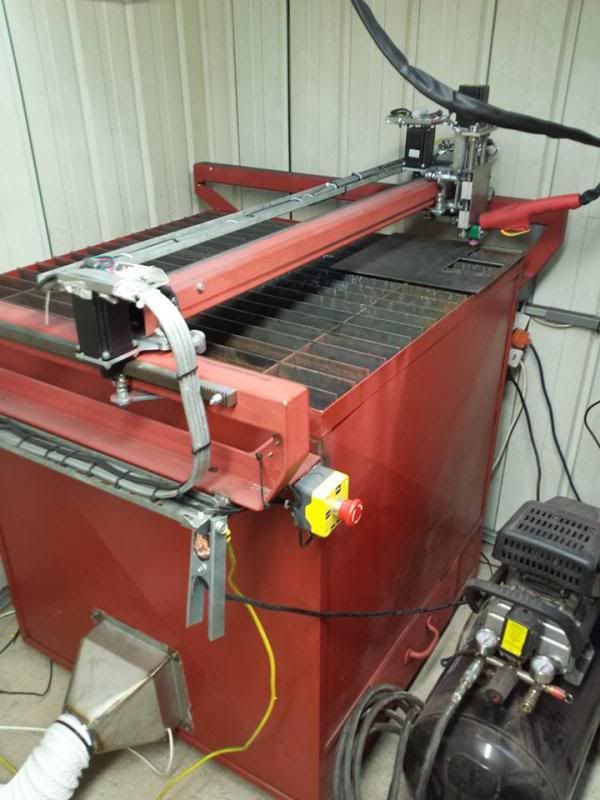
70.65 mm or travel. I used mach3 axis calibration to set the steps per unit which gave me the motor tuning step per unit of x axis 22.52234371 velocity 6000 acceleration 1000, y axis 23.7073022 velocity 6000 acceleration 1000.
I'm not using a thc yet but have a floating z axis i'm useing sheetcam to setup my dfx files. I'm useing 2 steppers motors on my x axis gantry now instead of slaving them togeather using mach3 iv took the wires from the x axis
breakout board and put the in to two TB6600hg drivers like in parallel. Iv cut the zigzag test and the picture iv upload is the result and the other is of the holes im trying to cut 16mm and a 50mm in the centre hope you understand what iv put as im terrible at explaining myself.
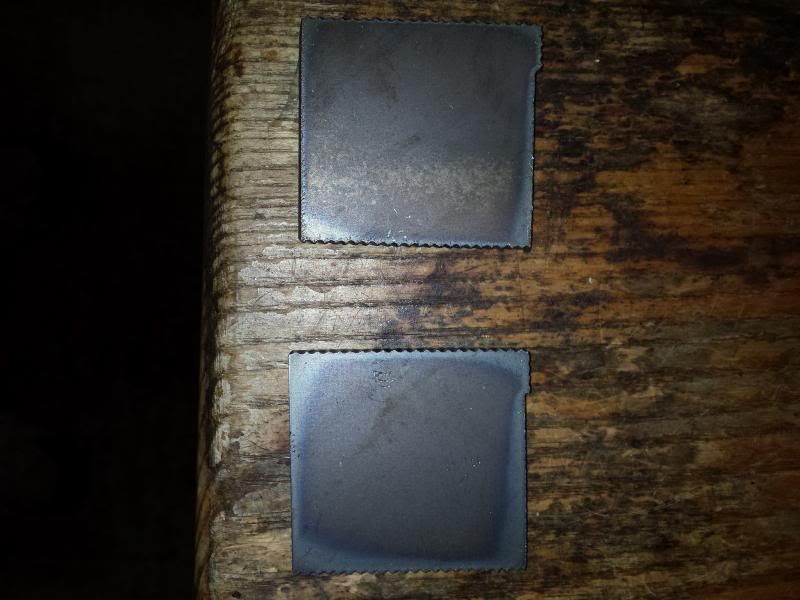
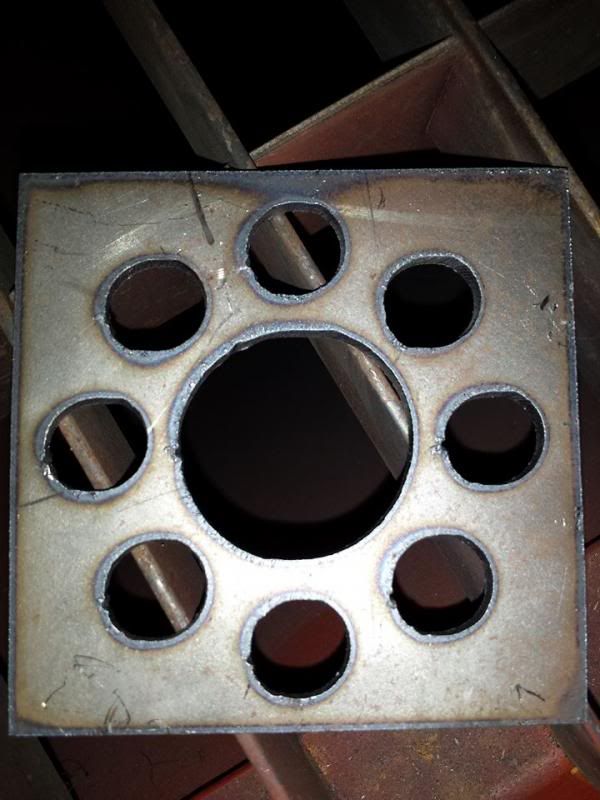
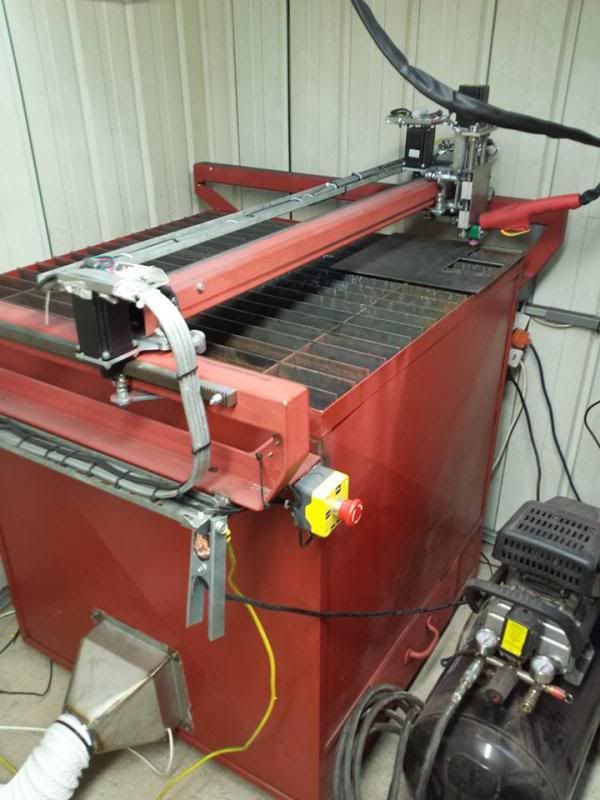
-
- 2.5 Star Member
- Posts: 212
- Joined: Sun Dec 01, 2013 1:29 pm
Re: think im loseing steps
Your holes dont look to bad from what I've seen. I assume the offset on the zig zag cutout is your start and stop points. If so the zig zag cut does look like you are loosing steps. What is your feed rate and material thickness? I had a similar problem when my acceleration was set too high. Try moving the acceleration in half. If your lost steps goes away then move it back up at small increments and see what happens. I know how frustrating this can be.
Precision Plama LLC SDB 5x10
CandCNC
Hypertherm 65
Mach3
SheetCAM
the GIMP
inkscape
QCAD
https://www.facebook.com/burtonskustom
CandCNC
Hypertherm 65
Mach3
SheetCAM
the GIMP
inkscape
QCAD
https://www.facebook.com/burtonskustom
-
- 1 Star Member
- Posts: 11
- Joined: Mon Nov 11, 2013 9:27 pm
- Location: March uk
Re: think im loseing steps
you are correct that is my start and stop place material is 3mm and feed rate one was 500mm/min and the other was 1000mm/ min feed rate allso the one with the holes the out side square is not 100% sqaure is got around a 3mm run of out of shape 100x100mm square.
-
- 4.5 Star Member
- Posts: 1504
- Joined: Fri Jan 18, 2013 3:19 am
Re: think im loseing steps
It's not a misquote.BTA Plasma wrote:I believe alot of folks misquote Tom from CandCNC using this same line.
The particular information submitted by Tom was clearly saying 1 inch of linear travel for 1 revolution of the stepper motor, and the reduction gearing ratio should be such that it gives that. The particular notes I read did not even mention the pitch diameter of the gear. Maybe you think I am quoting something else Tom said.
I realise this is a generalisation and can vary a bit from a much smaller motor to a much bigger one. This general rule was Toms experience after testing on many tables. However, surely with a 10:1 ratio the stepper has to run more than 3 times as fast as 3:1 ratio to get the same linear speed. At that speed the torque is way down from what it could be and a reversal of direction is going to take longer because of the necessary reduction in acceleration and deceleration, and the time alone needed to get the rpm down and back up again.
2500 x 1500 water table
Powermax 1250 & Duramax torch (because of the new $$$$ync system, will buy Thermal Dynamics next)
LinuxCNC
Sheetcam
Alibre Design 3D solid modelling
Coreldraw 2019
Powermax 1250 & Duramax torch (because of the new $$$$ync system, will buy Thermal Dynamics next)
LinuxCNC
Sheetcam
Alibre Design 3D solid modelling
Coreldraw 2019
-
- 1 Star Member
- Posts: 11
- Joined: Mon Nov 11, 2013 9:27 pm
- Location: March uk
Re: think im loseing steps
Need some help please im going to start all from scratch in need some help with motor tuning i,m useing nema 23 in 300oz 1.8 step angle direct mod 1.5 rack and 15 tooth 22.5 dp pinion TB6600hg drivers 1/8 ,can some one explain to me how to work out my step for the motor tuning please as i'm not understanding it all useing rack and pinion thanks all for your help so far
-
- 4.5 Star Member
- Posts: 1504
- Joined: Fri Jan 18, 2013 3:19 am
Re: think im loseing steps
OK Spooky, I'll give it a shot, but don't blame me if I get it wrong (there's my disclaimer done LOL).
First of all the size & torque of your motor are irrelevant for calculating the steps per inch (assuming Mach is using inches).
I Googled and found the tooth pitch of a 1.5 module rack is 4.7124 mm. You've got 15 teeth on your pinion so 1 revolution of your pinion will give you a linear travel of 15 x 4.7124 = 70.686 mm. Some people get into the pitch diameter of the spur gear, pi, etc, etc, but that's just complicating things as far as I'm concerned. The teeth are locked together and as long as you have the tooth pitch distance of the rack, you simply multiply that by the number of teeth on your spur gear to get the linear distance travel for one spur gear revolution.
In inches that is 70.686 / 25.4 = 2.7829 inches of linear travel for one revolution of your stepper motor.
You didn't mention any microstepping so at 1.8 degrees of motor revolution for one step pulse, you need 200 step pulses from Mach turn the motor one revolution.
200 step pulses divided by 2.7829 inches of travel = 71.867 steps per inch with your direct drive (and no microstepping) setup.
I Googled your drive and the datasheet mentioned it is a microstepping drive. However, didn't have time to go through the datasheet and see if it has a fixed microstep number. Whatever the microstep number is, multiply 71.867 steps per inch by that number, then use the new number as your steps per inch in Mach.
If you end up doing a pulley reduction system, then as an example if you had a 3:1 reduction, you would simply multiply 71.867 by 3 to give 215.6 steps per inch. But don't forget that is without any microstepping taken into account.
Hope that helps,
Keith.
First of all the size & torque of your motor are irrelevant for calculating the steps per inch (assuming Mach is using inches).
I Googled and found the tooth pitch of a 1.5 module rack is 4.7124 mm. You've got 15 teeth on your pinion so 1 revolution of your pinion will give you a linear travel of 15 x 4.7124 = 70.686 mm. Some people get into the pitch diameter of the spur gear, pi, etc, etc, but that's just complicating things as far as I'm concerned. The teeth are locked together and as long as you have the tooth pitch distance of the rack, you simply multiply that by the number of teeth on your spur gear to get the linear distance travel for one spur gear revolution.
In inches that is 70.686 / 25.4 = 2.7829 inches of linear travel for one revolution of your stepper motor.
You didn't mention any microstepping so at 1.8 degrees of motor revolution for one step pulse, you need 200 step pulses from Mach turn the motor one revolution.
200 step pulses divided by 2.7829 inches of travel = 71.867 steps per inch with your direct drive (and no microstepping) setup.
I Googled your drive and the datasheet mentioned it is a microstepping drive. However, didn't have time to go through the datasheet and see if it has a fixed microstep number. Whatever the microstep number is, multiply 71.867 steps per inch by that number, then use the new number as your steps per inch in Mach.
If you end up doing a pulley reduction system, then as an example if you had a 3:1 reduction, you would simply multiply 71.867 by 3 to give 215.6 steps per inch. But don't forget that is without any microstepping taken into account.
Hope that helps,
Keith.
2500 x 1500 water table
Powermax 1250 & Duramax torch (because of the new $$$$ync system, will buy Thermal Dynamics next)
LinuxCNC
Sheetcam
Alibre Design 3D solid modelling
Coreldraw 2019
Powermax 1250 & Duramax torch (because of the new $$$$ync system, will buy Thermal Dynamics next)
LinuxCNC
Sheetcam
Alibre Design 3D solid modelling
Coreldraw 2019
-
- 1 Star Member
- Posts: 11
- Joined: Mon Nov 11, 2013 9:27 pm
- Location: March uk
Re: think im loseing steps
Thats great now i understand just like to say a big thanks to every one for there input hopefully this will go a long way into helping my plasma table cut a lot better, I made the mistake of buying rubbish of flee bay think im going to buy a CNC Gecko G540 Stepper Motor Driver as iv heard a lot of bad things from these tb6600hg like only giving out 30% max torque and wrong microstepping data
-
- 4.5 Star Member
- Posts: 1504
- Joined: Fri Jan 18, 2013 3:19 am
Re: think im loseing steps
Gecko drives are great.
My table still has the Chinese "Smooth" (smooth really is a joke) brand stepper motors I got in the beginning. Horrid things that my Leadshine drive just could not run above a certain low rpm. Got Gecko G203V drives and they manage to run my crappy steppers all the way up to full rpm with a load on.
I was on a budget and tried to go cheap but in the end if you can buy quality, you buy it once and just don't have problems.
Keith.
My table still has the Chinese "Smooth" (smooth really is a joke) brand stepper motors I got in the beginning. Horrid things that my Leadshine drive just could not run above a certain low rpm. Got Gecko G203V drives and they manage to run my crappy steppers all the way up to full rpm with a load on.
I was on a budget and tried to go cheap but in the end if you can buy quality, you buy it once and just don't have problems.
Keith.
2500 x 1500 water table
Powermax 1250 & Duramax torch (because of the new $$$$ync system, will buy Thermal Dynamics next)
LinuxCNC
Sheetcam
Alibre Design 3D solid modelling
Coreldraw 2019
Powermax 1250 & Duramax torch (because of the new $$$$ync system, will buy Thermal Dynamics next)
LinuxCNC
Sheetcam
Alibre Design 3D solid modelling
Coreldraw 2019
-
- 1 Star Member
- Posts: 11
- Joined: Mon Nov 11, 2013 9:27 pm
- Location: March uk
Re: think im loseing steps
Just an update, Things are a lot better not perfect but a lot better one problem iv found was my y axis pinion wasen't meshed together good enough so had a lot of backlash but if i put it closer in the axis wobbled due to the pinion hole being a metric 6.5 mm instead of 1/4 but even with the backlash taken out this is the result oh and the messed up hole is due to dros on me tip and moving the plate around. 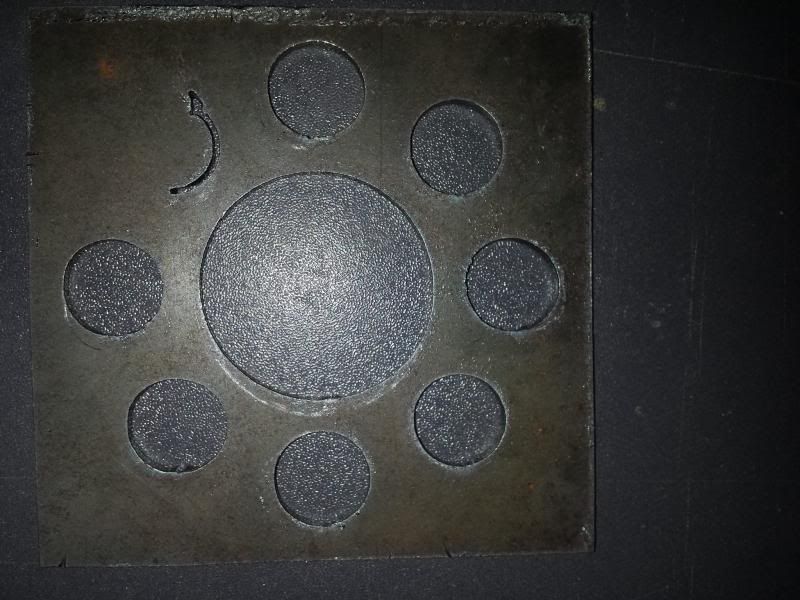
zigzag test is a lot better but still looks a little out on start and stop but hardly noticable so i think now with the new 540 geckos and the 3-1 reduction plus the thc i will be good thanks beefy and every one for the help.
Nigel
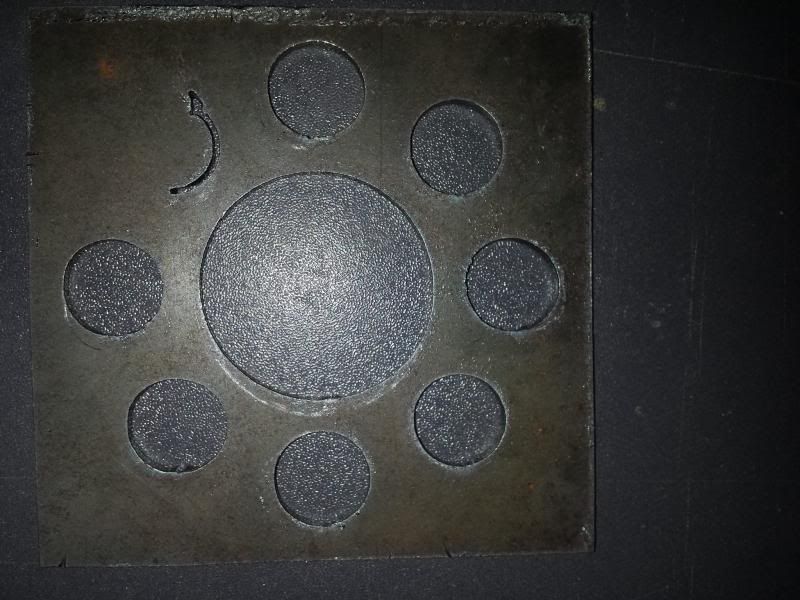
zigzag test is a lot better but still looks a little out on start and stop but hardly noticable so i think now with the new 540 geckos and the 3-1 reduction plus the thc i will be good thanks beefy and every one for the help.
Nigel
-
- 4.5 Star Member
- Posts: 1504
- Joined: Fri Jan 18, 2013 3:19 am
Re: think im loseing steps
Spooky,
if you go to the Gecko website they have a section where you can download some PDF files which will help you understand about steppers, drives AND just as important the power supply. With a reduction drive your steppers will be running at a higher rpm. This creates a back EMF which effectively means a higher voltage is needed to push the same amount of motor current as the rpm increases. Your power supply needs to give a high enough voltage to maintain motor winding current at the max rpm you expect, otherwise your motor torque will be less than what it could be, and remember at higher rpm, a stepper torque reduces anyway, so you don't want further reduction caused by a too low votage PS.
Keith.
if you go to the Gecko website they have a section where you can download some PDF files which will help you understand about steppers, drives AND just as important the power supply. With a reduction drive your steppers will be running at a higher rpm. This creates a back EMF which effectively means a higher voltage is needed to push the same amount of motor current as the rpm increases. Your power supply needs to give a high enough voltage to maintain motor winding current at the max rpm you expect, otherwise your motor torque will be less than what it could be, and remember at higher rpm, a stepper torque reduces anyway, so you don't want further reduction caused by a too low votage PS.
Keith.
2500 x 1500 water table
Powermax 1250 & Duramax torch (because of the new $$$$ync system, will buy Thermal Dynamics next)
LinuxCNC
Sheetcam
Alibre Design 3D solid modelling
Coreldraw 2019
Powermax 1250 & Duramax torch (because of the new $$$$ync system, will buy Thermal Dynamics next)
LinuxCNC
Sheetcam
Alibre Design 3D solid modelling
Coreldraw 2019