I am curious to know if anyone here has converted their growth series over to something other than the standard drive screw setup.
It doesn't look to be that difficult but then again I haven't built my own yet.
Anyone ever converted Torchmate to ballscrews?
-
- 4 Star Member
- Posts: 950
- Joined: Thu Jan 02, 2014 6:33 pm
Anyone ever converted Torchmate to ballscrews?
Torchmate 2x2 - Flashcut
Powermax 45 - Machine torch
Taig CNC Mill - Flashcut
Razorweld Distributor
Powermax 45 - Machine torch
Taig CNC Mill - Flashcut
Razorweld Distributor
-
- 5 Star Elite Contributing Member
- Posts: 3087
- Joined: Mon Jul 20, 2009 11:18 pm
- Location: North Carolina
Re: Anyone ever converted Torchmate to ballscrews?
Ballscrews likely will be heavier, potentially affecting inertia. Torchmates have tiny, undersized motors to start with, so this could cause issues.
Jim
Jim
-
- 4 Star Member
- Posts: 950
- Joined: Thu Jan 02, 2014 6:33 pm
Re: Anyone ever converted Torchmate to ballscrews?
The first ones did but they upgraded down the line.jimcolt wrote:Ballscrews likely will be heavier, potentially affecting inertia. Torchmates have tiny, undersized motors to start with, so this could cause issues.
Jim
Mine I think are 454oz motors
Torchmate 2x2 - Flashcut
Powermax 45 - Machine torch
Taig CNC Mill - Flashcut
Razorweld Distributor
Powermax 45 - Machine torch
Taig CNC Mill - Flashcut
Razorweld Distributor
-
- 4 Star Elite Contributing Member
- Posts: 1364
- Joined: Tue Feb 28, 2012 6:47 pm
Re: Anyone ever converted Torchmate to ballscrews?
Do some math. Take the max motor RPM (use like 800 to be generous) and divided it in half to keep the motor in its linear torque range . Now divide that by the TPI of the ballscrew. That will be your max CUTTING SPEED where you still have some residual acceleration left to do corners. If you have more than 2 TPI you probably cannot hit acceptable speeds for plasma cutting. You can get multi start ballscrews but they are $$$.
If you can make the speeds you need for thinner material then figure out how you are going to keep plasma smoke/dust off the ballscrews. They are precision bearings and do not handle the grit of plasma dust well. The one thing you get with ballscrews versus Acme lead screws is a much higher efficiency (up to double what an acme with anti backlash has) so they are easier to spin BUT as Jim points out they have more mass so the rotary inertia is higher.
I am not sure what your goal is but you need to weigh that versus the expense and changes you will need to make in the protection of the screws for whatever improvement you are seeking.
There is a compelling reason that most plasma tables you see have rack and pinion for the linear drive.
If you can make the speeds you need for thinner material then figure out how you are going to keep plasma smoke/dust off the ballscrews. They are precision bearings and do not handle the grit of plasma dust well. The one thing you get with ballscrews versus Acme lead screws is a much higher efficiency (up to double what an acme with anti backlash has) so they are easier to spin BUT as Jim points out they have more mass so the rotary inertia is higher.
I am not sure what your goal is but you need to weigh that versus the expense and changes you will need to make in the protection of the screws for whatever improvement you are seeking.
There is a compelling reason that most plasma tables you see have rack and pinion for the linear drive.
-
- 4 Star Member
- Posts: 950
- Joined: Thu Jan 02, 2014 6:33 pm
Re: Anyone ever converted Torchmate to ballscrews?
I have been trying to figure out how to mount the rack and pinion option but no luck yet.
If I had to get larger motors it's not a huge deal.
Is an acme screw the same as a ballscrew?
What do you think would be the best option to upgrade this torchmate to?
If I had to get larger motors it's not a huge deal.
Is an acme screw the same as a ballscrew?
What do you think would be the best option to upgrade this torchmate to?
Torchmate 2x2 - Flashcut
Powermax 45 - Machine torch
Taig CNC Mill - Flashcut
Razorweld Distributor
Powermax 45 - Machine torch
Taig CNC Mill - Flashcut
Razorweld Distributor
- _Ogre
- 3.5 Star Member
- Posts: 529
- Joined: Sun Sep 15, 2013 4:26 pm
- Location: Motown
Re: Anyone ever converted Torchmate to ballscrews?
not even closegamble wrote:Is an acme screw the same as a ballscrew?
acme screw thread is what is used on vices and c-clamps and uses a simple nut cut to match
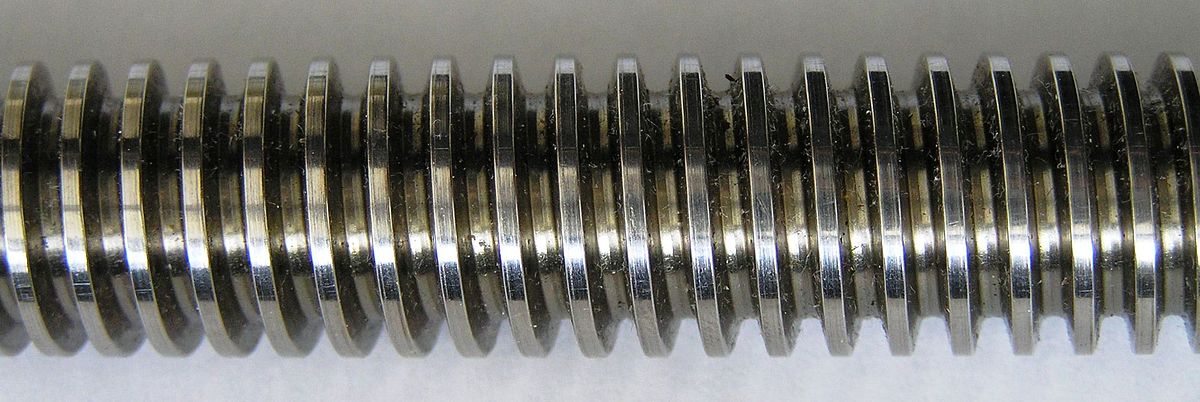
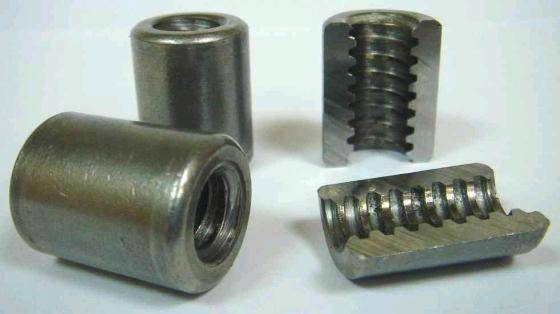
ball screws have lubricated balls

bulltear 4x8 cnc plasma table, candcnc bladerunner w/dthc, hypertherm powermax 65, sheetcam, mach3
laser cross hair for hypertherm torch http://www.plasmaspider.com/viewtopic.php?f=6&t=12508
an ogre smiley
how cool!
laser cross hair for hypertherm torch http://www.plasmaspider.com/viewtopic.php?f=6&t=12508
an ogre smiley

-
- 4 Star Elite Contributing Member
- Posts: 1364
- Joined: Tue Feb 28, 2012 6:47 pm
Re: Anyone ever converted Torchmate to ballscrews?
I am still trying to figure out what parameter of the table you want to improve by upgrading ?What do you think would be the best option to upgrade this torchmate to?
Ballscrews have LOTS less friction than an ACME leadscrew. BUT you are not going to improve your resolution unless you go to a ballscrew with more TPI than what you have, and then you will find the max speeds go DOWN. In my estimation its a small amount of gain for a lot or expense and work.
-
- 4 Star Member
- Posts: 950
- Joined: Thu Jan 02, 2014 6:33 pm
Re: Anyone ever converted Torchmate to ballscrews?
So what would be needed to increase the overall speed of the table? And something that I can use to ramp up speeds quicker?tcaudle wrote:I am still trying to figure out what parameter of the table you want to improve by upgrading ?What do you think would be the best option to upgrade this torchmate to?
Ballscrews have LOTS less friction than an ACME leadscrew. BUT you are not going to improve your resolution unless you go to a ballscrew with more TPI than what you have, and then you will find the max speeds go DOWN. In my estimation its a small amount of gain for a lot or expense and work.
Also all the rack/pinions I see are around a 22 or 44". I can't wrap my head around on how you can get 24 or 48" of travel on something that isn't even that large.
I haven't found a machine 4x4 that I want next that I can use all my existing controller, motors and software for. So thinking about building one but my first thought is upgrading the one I have.
Torchmate 2x2 - Flashcut
Powermax 45 - Machine torch
Taig CNC Mill - Flashcut
Razorweld Distributor
Powermax 45 - Machine torch
Taig CNC Mill - Flashcut
Razorweld Distributor
-
- 4 Star Elite Contributing Member
- Posts: 1364
- Joined: Tue Feb 28, 2012 6:47 pm
Re: Anyone ever converted Torchmate to ballscrews?
To increase speed on a table with lead screws :
1. Decrease the thread per inch count with new courser leadscews
2. Get leadscrews that are multi-start.
3. add belt pulleys to step up the RPM
4. Switch to Servo motors that have more inherent RPM
Options 1 - 3 MAY need higher torque motors because you sacrifice torque when you increase speed
Rack an pinion can be "spliced". The rack is usually cut so a butt joint works but is easy to check by taking a short length of rack and using it to get the mesh right at the joints. TO get longer lengths of rack contact Standard Steel Specialties.
1. Decrease the thread per inch count with new courser leadscews
2. Get leadscrews that are multi-start.
3. add belt pulleys to step up the RPM
4. Switch to Servo motors that have more inherent RPM
Options 1 - 3 MAY need higher torque motors because you sacrifice torque when you increase speed
Rack an pinion can be "spliced". The rack is usually cut so a butt joint works but is easy to check by taking a short length of rack and using it to get the mesh right at the joints. TO get longer lengths of rack contact Standard Steel Specialties.