How to prevent plate warpage
-
- 2 Star Member
- Posts: 75
- Joined: Sat Jul 19, 2014 10:24 pm
How to prevent plate warpage
I have been cutting plate ranging from 3/16" to 3/8" for skid steer attachments. I will nest a 4x8 or 5x10 sheet with various sizes, some being large rectangles to small brackets. The large pieces end up warping during the cut. The pieces will bow upward on the ends away from the slats. My THC compensates, but it sure makes it difficult to fit up and get straight again. I have tried cutting on the lowest amperage and the highest (85A) without luck. I have also run the water level at the bottom of the plate and about 1" below without much change. I have also tried pausing in between cuts for a while. This may have helped a bit. Since the ends are bowing up it seems that the top of the plate is staying cooler than the bottom. I thought about preheating the entire plate with a torch, but that would be time consuming. Any ideas on how to prevent this?
LDR 5x10
Hypertherm 85
Hypertherm 85
-
- 2.5 Star Member
- Posts: 194
- Joined: Sun Feb 26, 2012 1:42 pm
Re: How to prevent plate warpage
does it always happen? with water in the table, at proper speed i dont see how you are getting any warpage on plate thickness. i would think it has more to do with your supply of material.
i have no issue cutting any material down to even 14g with close cut tolerance
if it is infact warping, can you set cuts to minimize heat, so torch jumps around table not heating one location
i have no issue cutting any material down to even 14g with close cut tolerance
if it is infact warping, can you set cuts to minimize heat, so torch jumps around table not heating one location
-
- 2 Star Member
- Posts: 75
- Joined: Sat Jul 19, 2014 10:24 pm
Re: How to prevent plate warpage
Yes it happens every time. I may nest large rectangles (around 20" x 60-70") side by side. I can cut one out with slight warpage, stop the torch for a bit, then cut another and it will be worse. Thickness doesn't matter much....3/8" will pull up just like 3/16". I thought cutting faster, ie at 85 amps instead of 65, might help, but I don't think so. I've cut plate from the US, Sweden, Turkey, etc with the same results. It all has been hot rolled. I can't make the torch move around much because the pieces are nearly as long as the sheets themselves. I can stop the process, but that cuts into my productivity significantly.
The 14 ga that I cut hardly moves.
The 14 ga that I cut hardly moves.
LDR 5x10
Hypertherm 85
Hypertherm 85
-
- 3.5 Star Member
- Posts: 563
- Joined: Fri Jan 24, 2014 11:03 pm
Re: How to prevent plate warpage
Almost every sheet that I get isn't exactly straight. It has some bow / curve to it, and is that way from the mill. What I do is look at the material when I am racking it, and make sure to place all the bows facing the same direction, so that when they get put on the table they are all laying with the bow up. Now, when I lay them on the table, they flatten out and you can't tell just by looking at them, but you can sure tell when you have them in the air hanging by a plate clamp. I cut everything with the bow up, and some of them lift / pull a slight bit when they are cut, but always lay back down when they cool back off. I have found that cooling them off tends to "set" the deflection / deformation more so than letting them air cool on their own. I don't run a water table but down draft, even when I pull hot parts off the table I lay them on the floor or table like they were cut (bow up) and they always seems to go back to flat, or as close to it as they were going to be. This is most apparent when cutting AL, if you hit AL with cold air or water as soon as it is cut, it will stay warped all to hell, if you let it relax and cool on it's own it seems to return to flat no problem.
One other thing I have found to cut down on distortion / pulling when being cut, is to start in the middle of a long side, instead of on a corner. It seems to hold the plate and keep it from moving as much, resulting in parts that are truly square, and equal dimensions. If I start on a corner, some material seems to pull over to one side of the other as it's cut, and when the cut comes back to the corner where it started, it seems the plate "jumps" a little when it's cut loose, and one side / end will be off by a very small amount, (a 32nd of an inch or so) on large parts / plates. They also seem to bow up more / unevenly when I start on a corner, but when I start in the middle it seems more controlled and along one axis, so it bows, but doesn't twist as much.
Maybe the water is cooling the bottom of the plate / keeping it cooler and this is what is causing the large amount of bow along the top side. I would say try running the water a lot lower (low enough that it's not splashing on the plate if you can) and see what kind of a difference that makes. Also try placing the material on the table with the bow up, see if that doesn't help some.
Shane
One other thing I have found to cut down on distortion / pulling when being cut, is to start in the middle of a long side, instead of on a corner. It seems to hold the plate and keep it from moving as much, resulting in parts that are truly square, and equal dimensions. If I start on a corner, some material seems to pull over to one side of the other as it's cut, and when the cut comes back to the corner where it started, it seems the plate "jumps" a little when it's cut loose, and one side / end will be off by a very small amount, (a 32nd of an inch or so) on large parts / plates. They also seem to bow up more / unevenly when I start on a corner, but when I start in the middle it seems more controlled and along one axis, so it bows, but doesn't twist as much.
Maybe the water is cooling the bottom of the plate / keeping it cooler and this is what is causing the large amount of bow along the top side. I would say try running the water a lot lower (low enough that it's not splashing on the plate if you can) and see what kind of a difference that makes. Also try placing the material on the table with the bow up, see if that doesn't help some.
Shane
-
- 2 Star Member
- Posts: 75
- Joined: Sat Jul 19, 2014 10:24 pm
Re: How to prevent plate warpage
Thanks for the comments.
I too thought that the water may be cooling the bottom of the plate too much. But it seems if that were the case the middle of the pieces would bow upward. I have a decent grasp of physics, but it seems that the top of the plate is staying cooler and growing less than the bottom, which would cause the ends to bow up like a banana. I may try preheating the entire plate next time.
I will definitely look for a bow direction before I load the table up. I also will remove the cut pieces after cut so they will not be splashed and cooling by the adjacent cut.
I too thought that the water may be cooling the bottom of the plate too much. But it seems if that were the case the middle of the pieces would bow upward. I have a decent grasp of physics, but it seems that the top of the plate is staying cooler and growing less than the bottom, which would cause the ends to bow up like a banana. I may try preheating the entire plate next time.
I will definitely look for a bow direction before I load the table up. I also will remove the cut pieces after cut so they will not be splashed and cooling by the adjacent cut.
LDR 5x10
Hypertherm 85
Hypertherm 85
- Gamelord
- 4.5 Star Member
- Posts: 1637
- Joined: Wed Aug 29, 2012 5:17 pm
- Contact:
Re: How to prevent plate warpage
Are you running at exact book specs for your plate? I found if I am cutting too slow I get much more bow/warpage than if I cut faster. Book specs should give you the best results.
Once you take flight, your eyes will forever be turned to the sky." "Lack of appreciation is the worlds biggest crime."
Torchmate 6x14 w/THC Downdraft
Thermal Dynamics Cutmaster 101
Corel Draw / Adobe Illustrator
Torchmate CAD
Torchmate 6x14 w/THC Downdraft
Thermal Dynamics Cutmaster 101
Corel Draw / Adobe Illustrator
Torchmate CAD
-
- 2 Star Member
- Posts: 75
- Joined: Sat Jul 19, 2014 10:24 pm
-
- 2.5 Star Member
- Posts: 148
- Joined: Fri Jan 15, 2010 7:32 pm
Re: How to prevent plate warpage
You could try leaving some connecting tabs between parts. Say you are cutting rectangles side by side that are 90" long. Instead of cutting them all the way loose leave a 1/4" spot uncut about every 30" on the long sides which holds the whole sheet together and keeps things from moving around. Cut the whole sheet then go back and zap the tabs off with a cut wheel. Without doing that I will sometimes have trouble with long parts moving as cut but it's rare to have anything stay warped if the cut parameters are all correct.
-
- 5 Star Elite Contributing Member
- Posts: 3087
- Joined: Mon Jul 20, 2009 11:18 pm
- Location: North Carolina
Re: How to prevent plate warpage
Usually warpage means you are cutting too slow. Book specs for the Powermax85 are for best cut edge quality.....you may want to try cutting closer to the "max" speed.....a lot less heat input on the material, lower chance of warpage. I achieve the best results with a downdraft table (top and bottom of plate stay closer to same temp)....so you could try lowering your water so no be splashes on the bottom....maybe 8 or more inches below the material.
So....use the 65 amp process at up to 62 ipm on 3/8", or the 85 amp process at speeds up to 86 ipm, lower the water. Make sure your height is at .06" as well....too high and more heat inputs to the cut edge.
Jim Colt Hypertherm
So....use the 65 amp process at up to 62 ipm on 3/8", or the 85 amp process at speeds up to 86 ipm, lower the water. Make sure your height is at .06" as well....too high and more heat inputs to the cut edge.
Jim Colt Hypertherm
- SeanP
- 4 Star Member
- Posts: 950
- Joined: Thu Aug 01, 2013 11:50 am
- Location: Co Kerry, Ireland
Re: How to prevent plate warpage
Nice tip there Shane, I tried that today and it worked well, you automatically think starting on a corner would be best, I have been using thin wedges in the kerf sometimes to stop that 
Cheers

Cheers
Shane Warnick wrote:
One other thing I have found to cut down on distortion / pulling when being cut, is to start in the middle of a long side, instead of on a corner. It seems to hold the plate and keep it from moving as much, resulting in parts that are truly square, and equal dimensions.
Shane
Powermax XP45
Home built table, Candcnc DTHC 2, Dragoncut 620-4
R-Tech 210 Tig, Jasic 250 mig
Sheetcam, Scanything, Coreldraw
Table build gallery
Home built table, Candcnc DTHC 2, Dragoncut 620-4
R-Tech 210 Tig, Jasic 250 mig
Sheetcam, Scanything, Coreldraw
Table build gallery
-
- 3.5 Star Member
- Posts: 563
- Joined: Fri Jan 24, 2014 11:03 pm
Re: How to prevent plate warpage
SeanP wrote:Nice tip there Shane, I tried that today and it worked well, you automatically think starting on a corner would be best, I have been using thin wedges in the kerf sometimes to stop that
Cheers
Shane Warnick wrote:
One other thing I have found to cut down on distortion / pulling when being cut, is to start in the middle of a long side, instead of on a corner. It seems to hold the plate and keep it from moving as much, resulting in parts that are truly square, and equal dimensions.
Shane
I honestly never thought about using a wedge, I can see where I would always be chasing them down / fishing them out from under the table though.
I am glad it works for you, I have found that if I am cutting a square / rectangle, I will start about 1/3-1/4 of the way back from one corner, then when the cut starts, it only cuts 1/3 of that one side, then turns, cuts the other three sides, but there is still 2/3 of the side I started on holding the plate. Then it makes the last turn and starts back down the rest of the first side, the other three are already cut free, so the plate doesn't want to pull / push in any direction. Seems to keep the square parts even and truly square.
Shane
- tnbndr
- 4.5 Star Elite Contributing Member
- Posts: 1670
- Joined: Mon Jan 09, 2012 4:30 pm
- Location: New Berlin, WI
- Contact:
Re: How to prevent plate warpage
and make sure to place all the bows facing the same direction, so that when they get put on the table they are all laying with the bow up.
Can you clarify what "bow up" is. Assuming the raised ends of the sheet are facing up?
Dennis
LDR 4x8, Scribe, DTHCIV
Hypertherm PM45, Macair Dryer
DeVilbiss Air America 6.5HP, 80Gal., 175psi, Two Stage
16.9scfm@100psi, 16.0scfm@175psi
Miller 215 MultiMatic
RW 390E Slip Roll (Powered)
AutoCAD, SheetCAM, Mach 3
http://ikescreations.com
LDR 4x8, Scribe, DTHCIV
Hypertherm PM45, Macair Dryer
DeVilbiss Air America 6.5HP, 80Gal., 175psi, Two Stage
16.9scfm@100psi, 16.0scfm@175psi
Miller 215 MultiMatic
RW 390E Slip Roll (Powered)
AutoCAD, SheetCAM, Mach 3
http://ikescreations.com
-
- 2 Star Member
- Posts: 75
- Joined: Sat Jul 19, 2014 10:24 pm
Re: How to prevent plate warpage
I cut some pieces out of a 5 x 10 sheet of 3/8. I used the productions settings at 85 amps, I checked cut height, paused in between cuts, and loaded the material with the bow upward in the middle. The pieces themselves are pretty straight, but they were only 42" on the long side. The ends of the plate started lifting after a few cuts. Once I started cutting the sheet skeleton apart the bow was pretty severe, IMO (pic attached). I did start with the water much lower than what it is in the pic, but the smoke was terrible.
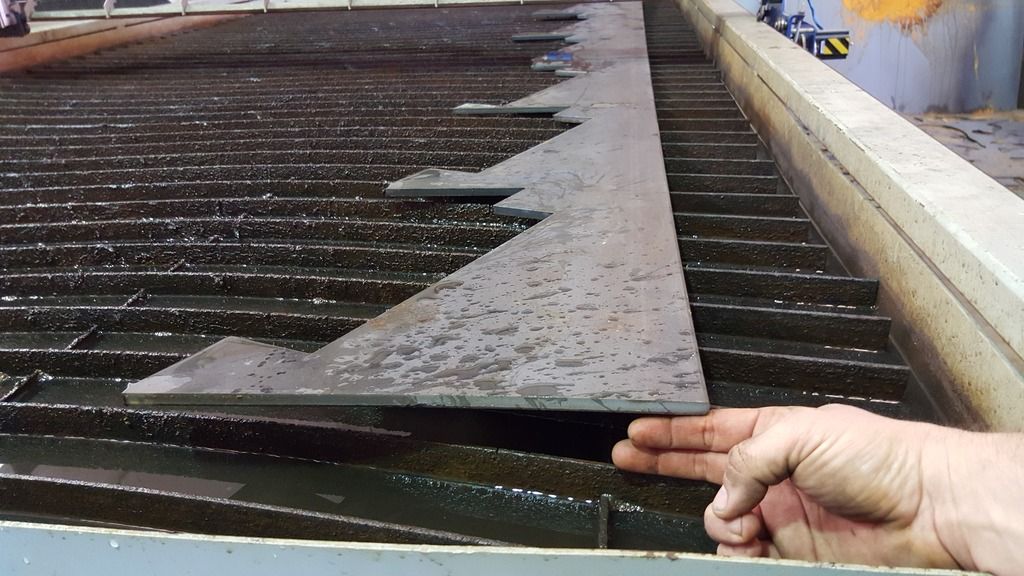
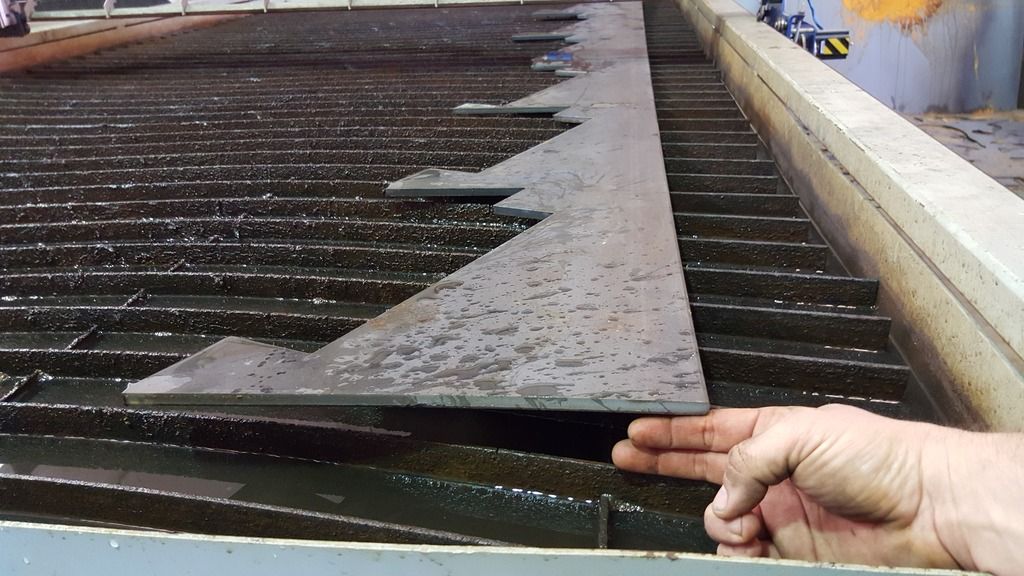
LDR 5x10
Hypertherm 85
Hypertherm 85
- acourtjester
- 6 Star Elite Contributing Member
- Posts: 7796
- Joined: Sat Jun 02, 2012 6:04 pm
- Location: Pensacola, Fla
Re: How to prevent plate warpage
It would be interesting to find out if there is a difference in this warping action for steel manufactured in a different location (countries). If the cooling process when it was rolled out has anything to do with the warping. I am in north Florida and I had steel from the Netherlands I would think western states have steel from China.
Raw Steel Production by Country (Thousand metric tons)
Rank Country World Production, By Country (Thousand metric tons)
1 China 489,240
2 Japan 120,203
3 United States 98,100
4 Russian Federation 72,389
Raw Steel Production by Country (Thousand metric tons)
Rank Country World Production, By Country (Thousand metric tons)
1 China 489,240
2 Japan 120,203
3 United States 98,100
4 Russian Federation 72,389
DIY 4X4 Plasma/Router Table
Hypertherm PM65 Machine Torch
Drag Knife and Scribe
Miller Mig welder
13" metal lathe
Small Mill
Everlast PowerTig 255 EXT
Hypertherm PM65 Machine Torch
Drag Knife and Scribe
Miller Mig welder
13" metal lathe
Small Mill
Everlast PowerTig 255 EXT
-
- 3.5 Star Member
- Posts: 563
- Joined: Fri Jan 24, 2014 11:03 pm
Re: How to prevent plate warpage
Opposite of what you are describing. The hump in the middle is up like a hill, the ends are cupped down. I find that parts seem (to me anyways) to raise less and stay flatter when I cut like this. The weight of the plate will flatten it out on the table, and I don't seem to have issues such as the original poster describes.tnbndr wrote:and make sure to place all the bows facing the same direction, so that when they get put on the table they are all laying with the bow up.
Can you clarify what "bow up" is. Assuming the raised ends of the sheet are facing up?
Shane
-
- 5 Star Elite Contributing Member
- Posts: 3087
- Joined: Mon Jul 20, 2009 11:18 pm
- Location: North Carolina
Re: How to prevent plate warpage
Some warpage is caused by heat input to the material (going too slow, height incorrect, etc.) while others are internal stresses of the plate being released when cuts are completed. The fact that your plates seem to have quite a bow to them tells me that there is internal stress. I would find a different steel provider.
Jim Colt
Jim Colt
-
- 2 Star Member
- Posts: 75
- Joined: Sat Jul 19, 2014 10:24 pm
Re: How to prevent plate warpage
I appreciate all of the comments. I talked to my steel supplier, and they have the same problem when cutting on their table. I thought about checking on cold rolled plate prices. Does anyone know if cold rolled would be less likely to warp.
LDR 5x10
Hypertherm 85
Hypertherm 85
-
- 2.5 Star Member
- Posts: 194
- Joined: Sun Feb 26, 2012 1:42 pm
Re: How to prevent plate warpage
cold rolled will be less likely to have internal stress as it is sized cold (hence the name),as far as i know. not sure how thick they go in cold rolled.
what area are you located? if it is happening to them as well, its definitely the material, and as stated, try a different place
what area are you located? if it is happening to them as well, its definitely the material, and as stated, try a different place
-
- 2.5 Star Member
- Posts: 181
- Joined: Wed Jan 20, 2010 6:55 pm
- Location: Canada
Re: How to prevent plate warpage
Interesting topic. I definitely think steel quality has a lot to do with plate warpage from cutting. Mostly I cut 3/8ths plate with a Powermax 1000 and a Duramax torch, 65 amp consumables, cutting according to chart settings. I have made a lot of what we call punch plates for screen decks in the aggregate business. These are made of SSAB hardox 450, who pride themselves in properly rolling their plates flat. These punch plates measure 48 x 74 inches and will have up to 220 six sided holes in them, and a lot of heat build up, yet they don't warp at all. Have also used A36 plate for other projects which if laid on table with the bowed side up don't lie flat. As you begin cutting from one end they slowly lie down. by the time a third of sheet is cut up it is flat on the table. Cutting longer rectangles can be tricky though. Sometimes i leave sheets outside with the bowed side up and the ends on wooden blocks if they are real bad. Seems like if left awhile the sheer weight of the sheet, heating and cooling cycles from day to night helps. Good luck!!!
-
- 3 Star Member
- Posts: 313
- Joined: Tue Jul 28, 2009 11:23 pm
- Location: Weiser, ID
- Contact:
Re: How to prevent plate warpage
The thickest CR Ive ever gotten is 10 gauge and often times it seems like 11 gauge is as thick as they like to carry in CR.
-
- 2 Star Member
- Posts: 75
- Joined: Sat Jul 19, 2014 10:24 pm
Re: How to prevent plate warpage
Just to update this thread a bit. I have been cutting skid steer buckets out of 3/16" A36. The latest plate isn't stamped with the country of origin, but this stuff is laying even after cutting large nested rectangles. I have been 85 amps at book specs with the water 1/2" below the plate. The 3/8" I cut was from Australia, and it did warp some. But it was much less than before. I am thinking steel quality is the culprit.
LDR 5x10
Hypertherm 85
Hypertherm 85
-
- 4 Star Member
- Posts: 1472
- Joined: Wed Feb 04, 2009 5:35 pm
Re: How to prevent plate warpage
Getting Australian steel nowadays is getting harder and harder. I try to wherever possible but unfortunately more and more of the iron ore we exported to China is coming back to us as sheet plate tube and bar stock.
I have found a lot of variation with imported steel from China and India, not just in the cutting but in fabrication and welding too. I know you will get it in any material but the malleability varies a lot within a sheet, it will bend much differently across the sheet to along it.
I'm told this is due to several factors starting right at the mill where different levels of quality control and differing operation processes are responsible. The Chinese are the masters of reverse engineering but as Jim will attest to, having a metallurgist provide a composition break down doesn't necessarily provide the required process specifications which can have a huge bearing on the final outcome. The forming process as well as the cooling process also affects the material greatly.
Most of the sheet and some of the plate is being imported as coils. The uncoiling and flattening process also affects the material to turn this into sheet form. Different steel companies are using different processes for this, some of which leave the material, especially the heavier stuff with a considerable bow in it. The closer to the centre of the coil, the more tightly this material is wound so without multiple rollers and high quality equipment this decoiling can have a big difference between the first and last sheet cut from the coil. Due to the difference across the coil/ sheet when this material is cut by something like we are doing with a plasma the outer areas or thinner width arts will distort (or try to return to their coiled state) more than other areas. Where this sheet was closer to the centre of the coil the memory to coiled will also be greater.
I have found that not all steel coming out of China is crap as they are the largest manufacturing country in the world and have some very modern facilities but these are normally at the higher end of the price scale so are not as attractive to many of the companies importing steel. These companies are generally price driven so will buy from wherever they can get it the cheapest, hence the crap being imported.
I will continue to pay a bit more at the raw material stage of the process and also continue to pay more for the labour component and more for any of the locally outsourced component so as to maintain as much local content as possible in the finished product and most of my customers are quite happy to pay more to keep things locally made. Some will buy the mass produced Chinese but then they are not really my customers.
One day we will be looking back explaining to our grandkids what a trade was and what it was like being able to be able to actually make something ourselves.
Murray
I have found a lot of variation with imported steel from China and India, not just in the cutting but in fabrication and welding too. I know you will get it in any material but the malleability varies a lot within a sheet, it will bend much differently across the sheet to along it.
I'm told this is due to several factors starting right at the mill where different levels of quality control and differing operation processes are responsible. The Chinese are the masters of reverse engineering but as Jim will attest to, having a metallurgist provide a composition break down doesn't necessarily provide the required process specifications which can have a huge bearing on the final outcome. The forming process as well as the cooling process also affects the material greatly.
Most of the sheet and some of the plate is being imported as coils. The uncoiling and flattening process also affects the material to turn this into sheet form. Different steel companies are using different processes for this, some of which leave the material, especially the heavier stuff with a considerable bow in it. The closer to the centre of the coil, the more tightly this material is wound so without multiple rollers and high quality equipment this decoiling can have a big difference between the first and last sheet cut from the coil. Due to the difference across the coil/ sheet when this material is cut by something like we are doing with a plasma the outer areas or thinner width arts will distort (or try to return to their coiled state) more than other areas. Where this sheet was closer to the centre of the coil the memory to coiled will also be greater.
I have found that not all steel coming out of China is crap as they are the largest manufacturing country in the world and have some very modern facilities but these are normally at the higher end of the price scale so are not as attractive to many of the companies importing steel. These companies are generally price driven so will buy from wherever they can get it the cheapest, hence the crap being imported.
I will continue to pay a bit more at the raw material stage of the process and also continue to pay more for the labour component and more for any of the locally outsourced component so as to maintain as much local content as possible in the finished product and most of my customers are quite happy to pay more to keep things locally made. Some will buy the mass produced Chinese but then they are not really my customers.
One day we will be looking back explaining to our grandkids what a trade was and what it was like being able to be able to actually make something ourselves.

Murray